The V-Series Rotary Air Dampener
We all know the importance of maintaining proper O2 levels with burners. Newer controls and linkageless controls definitely have improved your ability to control O2. Advances have also been made with O2 trim, and the O2 sensors have become more reliable and a little less costly. Therefore, the burner manufacturer has the ability to make improvements in the basic design of the air dampers to make a huge improvement in operation.
Being hydronics people, we all remember seeing a V-port ball valve for the first time. We will not explore the more linear nature of this design over the standard ball valve, but air foil air damper technology is similar. |
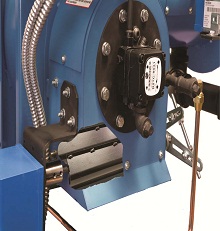 |
Consider a typical flat damper O2 curve. When the dampers first open, there is a big inrush of air, causing percent O2 to increase. By simply changing these dampers to a rotary drum damper, or even more cost effectively, by utilizing an airfoil design damper, this inrush of air is minimized. |
Remember, few boilers operate at 100% load – and often run at 25%-50%, so the goal should be to optimize O2 at those operating points. You can see on the Airfoil blade curve, O2 levels immediate start to decrease as the damper opens, while the flat blade damper immediately starts to increase. |
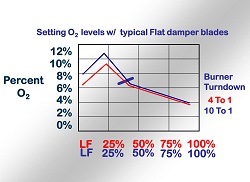 |
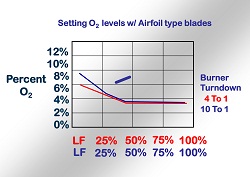 |
|
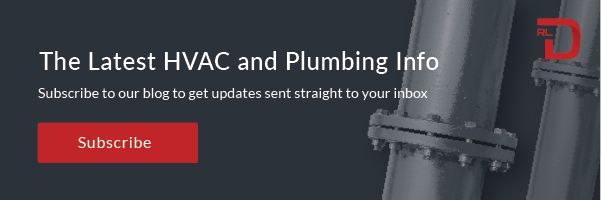 |
Disclaimer: R. L. Deppmann and it’s affiliates can not be held liable for issues caused by use of the information on this page. While the information comes from many years of experience and can be a valuable tool, it may not take into account special circumstances in your system and we therefore can not take responsibility for actions that result from this information. Please feel free to contact us if you do have any questions.