with edit by Norm Hall
Last week we defined turndown ratio. Turndown ratio is defined as the ratio of the maximum input to the minimum input. It is an expression that translates to a minimum percentage of firing rate the appliance is designed to operate at. The ability to modulate infinitely from the minimum to the maximum translates to improved seasonal efficiency by being able to match the actual load requirements.
The vast majority of systems rarely operate at the design temperature, since most of the time the system is at part load. In fact, ASHRAE (American Society of Heating, Refrigerating and Air Conditioning Engineers) publishes what is called “Bin” weather data. This report identifies the amount of hours a specified location experiences varying outdoor temperatures for a given geographic area.
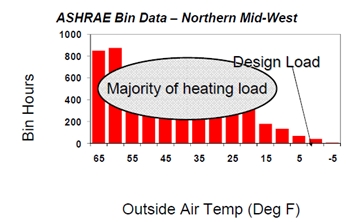
This information helps us to understand the amount of time that the system operates in the Part Load condition. This information will help you in the evaluation of your final selection and optimum turndown ratio for a project using condensing boilers. For example, the Aerco Benchmark BMK-2.0 boiler has a design input of 2,000,000 BTUH and has a 20:1 turndown ratio. In that case, it can modulate from 2,000,000 BTUH down to 100,000 BTUH WITHOUT having to cycle off and on to match the part load condition.
This cycling, in particular short cycling, can have dramatic affects on equipment, seasonal efficiency and carbon emissions.
• The equipment affects can include stress on the heat exchanger resulting in premature failure and (b) wear and tear on controls decreasing longevity.
• Seasonal efficiency is reduced by the extra cycles of pre-purge and post purge operation, wasting valuable heat to the atmosphere without return on investment.
• Carbon emissions (from start-up) are increased, due to the temperature overshooting that short cycling causes.
The ability of a high turndown boiler to match the Energy input to Actual Heating Load, contributes greatly improved seasonal efficiencies. The lower input potential will follow the inverse efficiency curve. Not only is less fuel burned, it results in better unit efficiency, since the heat transfer surface remains constant. Precise temperature control allows system designer to take full advantage of latest boiler and control technology offered by Aerco and Laars
For the design professional who is seeking sustainable solutions to their clients concerns, look no further than the condensing products offered by the R. L. Deppmann Company. Next week we will look at two examples. |